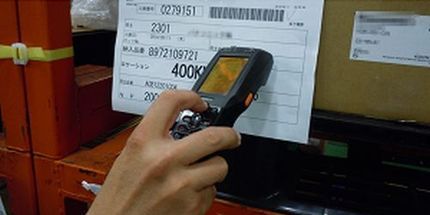
近年部品メーカー様においては、多品種の部品を小ロットや、頻度の高い納入が求められる傾向があるかと思われます。そのような中で組立工場様に、部品の誤出荷や数量過不足など納品ミスが発生すると信用の失墜、販売機会のロスにつながってしまいます。それを防ぐにはいかにミスをしない環境を作るかが必要です。
1.人の能力だけでは対応が難しい
例えば以前はピッキングリストと現物の品番の照合を目視で行っていたり、数量確認を手数えで行っていたために、作業員個人の能力に依存し作業品質は不安定になりがちでした。また客観的な作業履歴として残らないため精度向上の対策が遅れがちでした。
2.人の補助をする機能
人の能力や経験を補うには、データが必要です。例えばハンディターミナルを使用し品番照合を目視を介さずにピッキングすることで、誤出荷を防止する、計量機械を使用することで数量計測を自動化し、人の力を極力省くなどの取組みが有効になります。しかしシステム化を進めるだけではミスがゼロにならないことも現実です。
3.繰り返しの訓練とトレーサビリティ
いかにシステム化をしても、ミスをなくすには繰り返しのトレーニングが必要不可欠です。谷口運送では、毎日一人の作業者のピッキングを作業場のメンバー全員で確認し、その方法が正しいのか間違えなのか共有する時間を設けたり、定期的なミーティングの場で日常のヒヤリハットを確認し合うなどをし、日々作業精度の向上を目指しております。
また、ハンディターミナルにトレーサビリティの機能を持たせているので、部品メーカー様から組立工場様までの間で納品のトラブルがあった際に作業履歴の照会と情報提供を速やかに行うことができます。